Analysis of the behavior of the roller bearing impedance under different operating conditions
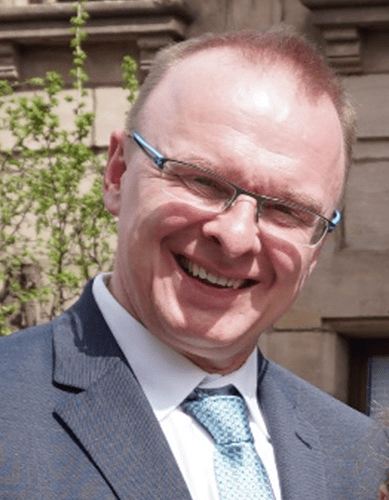
To investigate the behavior of the rolling bearing impedance and its applicability potential for condition monitoring, tests were carried out in cooperation with HCP Sence under different rotation speed and damage conditions.
Rolling bearings of type 6005-2RSH from SKF with the lubricant Mobil SHC Grease 681 WT were used as test objects. These test bearings were mounted on a shaft that was electrically insulated from the environment. A Fimra SEVA TEC type SEV-MX1-100L2-8 electric motor was used as the drive unit. A measuring device from HCP Sence was used to measure the impedance.
Various test were carried out in order to investigate the speed dependence of the impedance. Thereby, different speed levels from standstill to maximum engine speed were approached in a time interval of 10 minutes each. At the lower speeds, a smaller gradation was selected in order to include the transition from pure friction to fluid friction.

The results show that the rotation speed has an effect on the impedance and a change in speed also results in a proportional impedance response. When adjusting a speed, an overshoot or undershoot of the impedance occurred. However, the value converged to a stable value over time.
This behavior can be explained mainly by the change in bearing operating temperature.
The influence of temperature was especially evident in the endurance tests. In these, the rolling bearing was monitored at constant speed. There was a similar overshooting of the impedance at the beginning, which gradually went back to a stable value over time. This shows the temperature change of the bearing towards its operating temperature.
These correlations can be used successfully to monitor changes in the initial situation. However, more precise statements are needed in order to draw conclusions from the measured impedance or its curve about the bearing temperature or speed or other influences such as changes in load.

Two experiments were carried out to investigate the impedance behavior of a damaged bearing. In the first test, the occurrence of damage during operation was to be analyzed. For this purpose, the bearing was run at a constant speed for 3 hours and after 1.5 hours, the bearing was intentionally damaged on the outer ring.
The investigation of the impedance showed a clear change in the signal after the damage was applied. A distinctive signal noise was formed. This effect can be explained by the entry of particles into the lubricant and repeatedly rolled over the damaged area. Thereby, the lubricant film is disrupted and the capacitive behavior changes into ohmic behavior and leads to a drop of the impedance value.
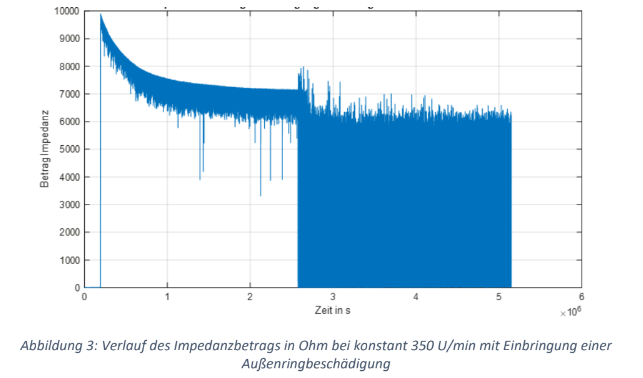
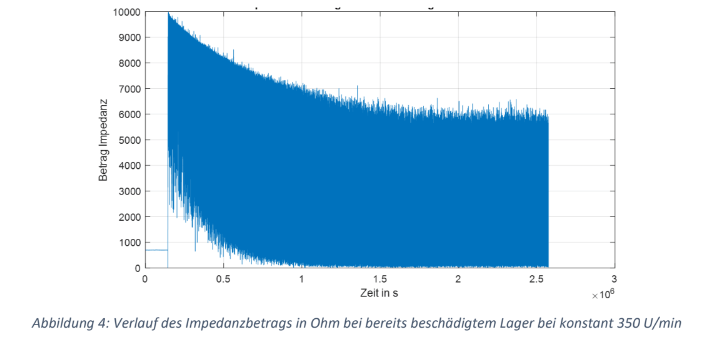
The second test was intended to detect an already damaged bearing after installation. For this purpose, the already damaged bearing was again run at a constant speed after a cooling phase. Here, the signal noise already seen in the preliminary test and the temperature-related drop in the impedance value occurred.
These results clearly indicate that the impedance monitoring can be used to detect damages. For a more precise statement on the applicability and comparability to the widespread structure-borne noise analysis, further tests with damaged inner ring and rolling elements would have to be carried out.