HCP-LubeSecure
lubrication monitoring
Bearing damage prevention through
lubrication monitoring
Only when a rolling bearing is correctly lubricated does it run safely and with low wear. This means that there must be a fully formed lubricant film at all times, which separates the metallic contact partners within the bearing from each other. If this is not the case, direct contact occurs, which causes the bearing to wear quickly and leads to damage.
Lubricating when needed
means
80 %
of bearing damage prevented
80 %
of bearing damage prevented
60 %
reduction in lubricant consumption
60 %
reduction in lubricant consumption
3-40 %
reduction of energy consumption
3-40 %
reduction of energy consumption
HCP Sense technology vs Current state of the art
Unfortunately, this cannot be monitored with conventional technology, which means that no knowledge of the dominant lubrication condition can be obtained. The sensor bearing from HCP Sense provides information about the lubrication and enables continuous monitoring.
With our impedance measurement, the electrical behavior of the rolling bearing can be monitored live on the machine. In the case of liquid friction, when there is a fully formed lubricant film and the metallic surfaces are separated, the bearing behaves electrotechnically like a capacitor. In the case of mixed and boundary friction, there is metallic contact and the bearing exhibits ohmic behavior as with an electrical resistor.
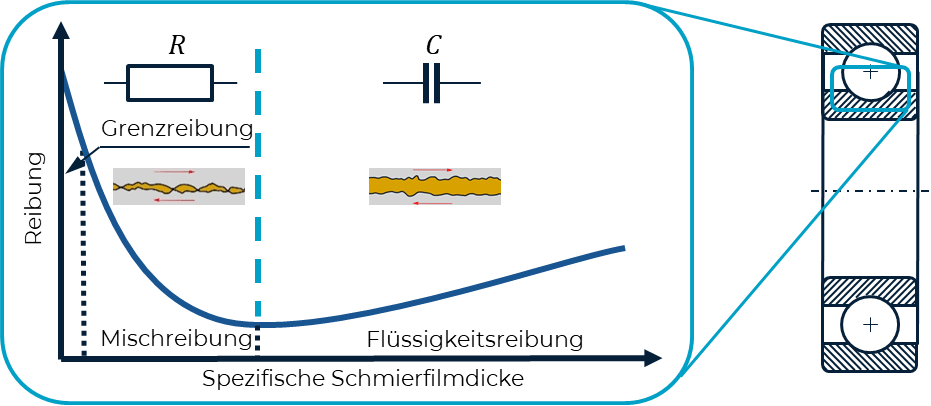
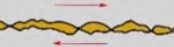
Insufficient lubrication
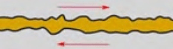
Optimal lubrication
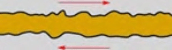
Over-lubrication
- Determine lubrication condition
- Avoid insufficient lubrication and damage
- Avoid overlubrication and energy consumption
- Optimal machine operation
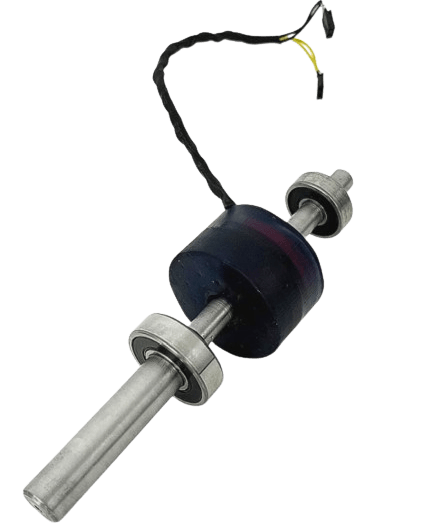
The advantages of our technology
With our technology you can prevent numerous damages.
Early damage detection
Over 75% of all rolling bearing damage can be traced back to lubrication failure. With our technology, you can detect these lubrication problems early enough to take countermeasures before increased wear leads to bearing damage.
Increased profit
With regard to predictive maintenance, our customers benefit massively by reducing planned downtime for maintenance purposes and avoiding unplanned downtime if a damage occurs.
Longer maintenance intervals
In addition, thanks to the continuous monitoring of the lubrication condition, maintenance intervals can be extended and agilely planned.
Discover now the other basic functions of our sensors.
Discover now the other basic functions
of our sensors.